RollerBall® Case Studies
Real-life examples where these innovative sorters are making a difference.
Package Sorting for Last-Mile Delivery
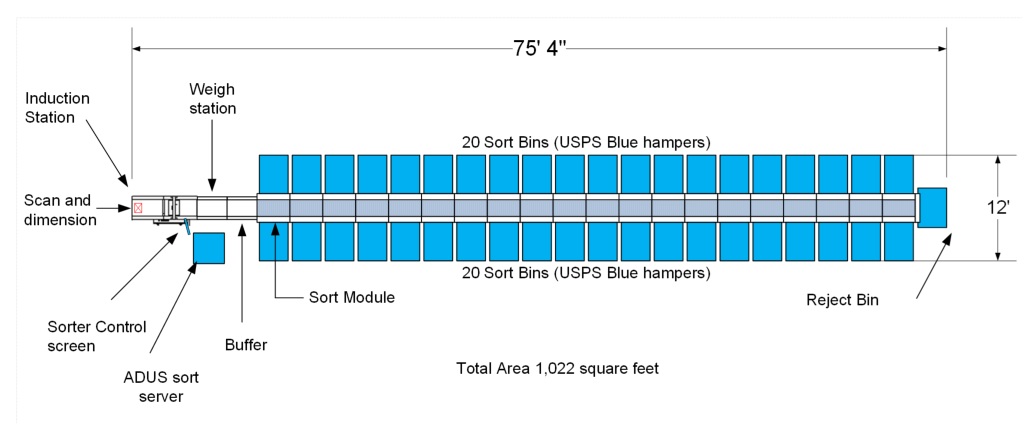
Installed in one day, operational on day two. This versatile sorter has been in daily operation since its April 2018 commissioning, and has already handled almost 4 million packages. Four more sort points were added months after installation. The new sorter section was installed, “plug-and-play”, in less than 4 hours. This system sorts a variety of boxes, bags, envelopes and pillow packs into hampers at rates of over 1,800 per hour.
- Compact footprint fits into a crowded delivery unit
- Quiet, dependable operation
- Intuitive operation, no significant training required
- Custom interface to Postal sorting server
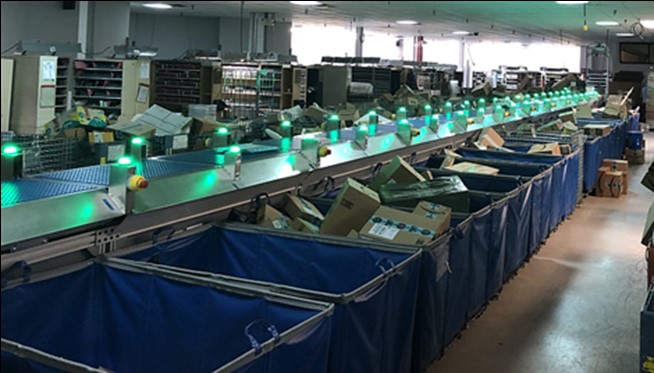
With minimal training, clerks quickly learned how to operate the sorter and became proficient in feeding the wide variety of packages and shapes. Illuminated touch buttons, illuminated scanner targets, and audible read confirmation make sorter operations intuitive.
Site personnel have been particularly pleased with the low noise level of the sorter and how the sorter will wait in standby, always ready to run whenever anyone had packages, even with a single operator.
Sorting Express Packages into Sacks
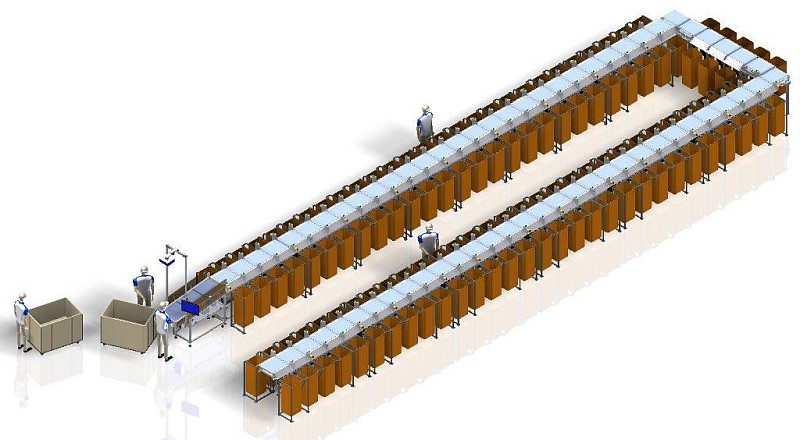
This application called for sorting envelopes and small parcels into sacks. Limited floor space required maximum efficiency from the sorter layout to fit over 120 sort separations into a very tight space.
The scanner reads a variety of barcodes, and a dimensioner measures the volume of each package to calculate and track the fullness of each sack. A scale is not needed in this application.
Smaller RollerBall® modules are used, arranged in a U-configuration.
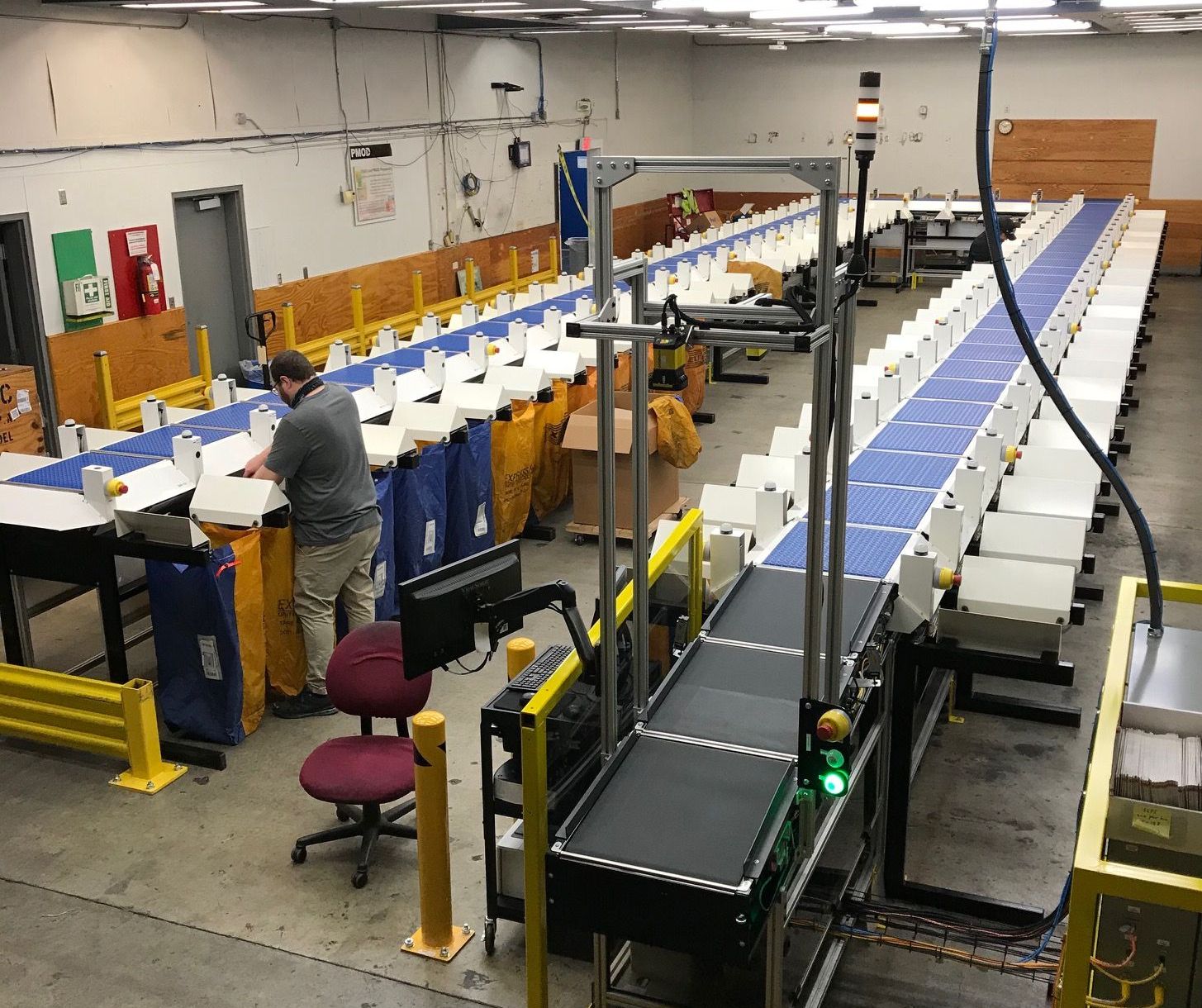
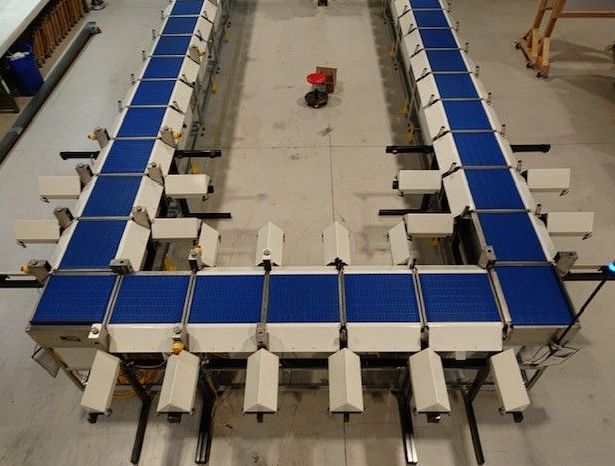
Two right angle turns are included for efficient use of space. These turns use RollerBall® modules to cleanly change package direction while maintaining sorter throughput.
Returns Processing
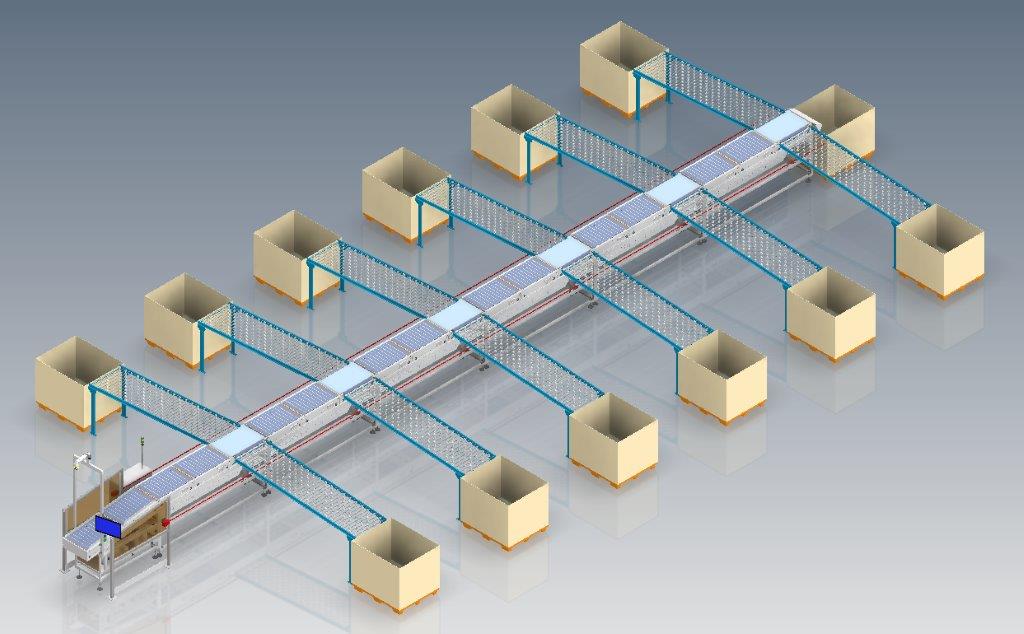
This example shows how “gapping” and “transfer” modules can be combined to create a sorter that spreads its sort points across a larger area.
This returns processing application sorts packages to gravity conveyor, rather than directly into containers. Line-full sensors detect when a particular runout is backed up.
Packages are faced and placed on the induct belt. An overhead scanner reads the return label, and the sorter communicates with the Warehouse Management System (WMS) to determine its sort destination. Each item is then routed to the appropriate transfer module.
The transfer modules are standard RollerBall® units. The gapping modules use the same powered rollers as the transfer modules, but with a simple belt as the conveyor surface for unidirectional motion.
Multiple gapping modules are provided between each of the transfer modules to allow room for manual access to each side of the skate wheel buffers, and to ensure that the runout locations match the facility layout. Each runout is equipped with a section of gravity conveyor with an end stop to accumulate product for manual packaging.
Routing and Applying Labels
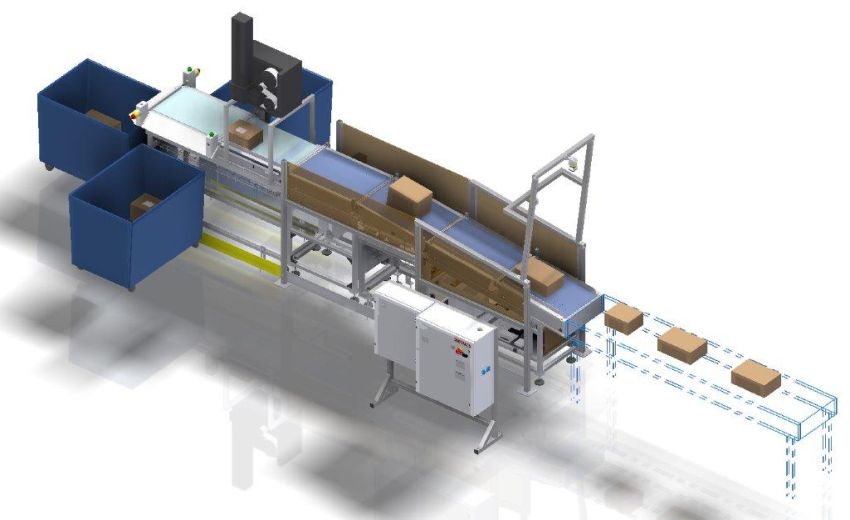
This sorter is designed for a micro-fulfillment operation. It includes scanning, weighing and labelling. This system integrates with shipper optimization software, to spread shipments across multiple shipping companies, and automatically sort by shipper.
The scanner reads an order number for each package, and looks it up in the manifest system. The weight of the package and its order information are used to determine shipper assignments. The appropriate shipping label is printed, applied and verified. The package is then sorted into hampers based on shipping provider and dispatch window.